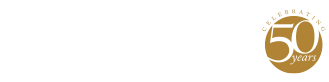
© 2024 GSI Ingranaggi S.r.l. - Via S. Quasimodo, 9 - 42023 Cadelbosco Sopra (RE) - P.Iva 00211250352 - NUM. REA RE-110195 - PEC: gsisrl@gigapec.it -
gsi@gsi-ingranaggi.it
Bando digitalizzazione |
Indice |
Privacy |
General Selling Conditions |
Informativa videosorveglianza |
Cookie Policy |
Cookie Setting